What is the most harsh environment for electronic components to operate in?
According to Paul Pickering of “Electronic Component News”, it’s Venus, where temperatures reach 500°C and the atmosphere contains clouds of sulfuric acid.
While most applications don’t require you to prepare connectors for space travel, the need for components that can withstand extreme or harsh environments is growing.
What Makes an Extreme Environment Extreme?
Temperature and Environment
Connectors for Low-Temperature Environments – When the temperature reaches the range of -55°C/-67°F to 150°C/302°F, it is considered an extreme temperature. Both extremely high and low temperatures can damage electronic systems.
Additionally, rain, water vapor, water immersion, as well as dust and dirt in indoor and outdoor environments, can cause harm to components.
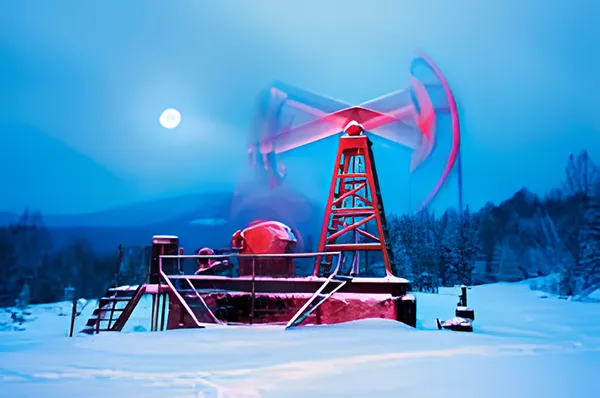
Pressure
Technologies for downhole and deepwater applications need to operate under extreme pressures. For example, pressures in deep-sea oil wells can exceed 20,000 psi.
“Downhole designs,” Pickering writes, “often place electronic equipment in a pressure vessel rather than expose it to such conditions.” The housings incorporate alloys like beryllium copper or inconel (a nickel/chromium/iron combination) that exhibit corrosion resistance at high temperatures.
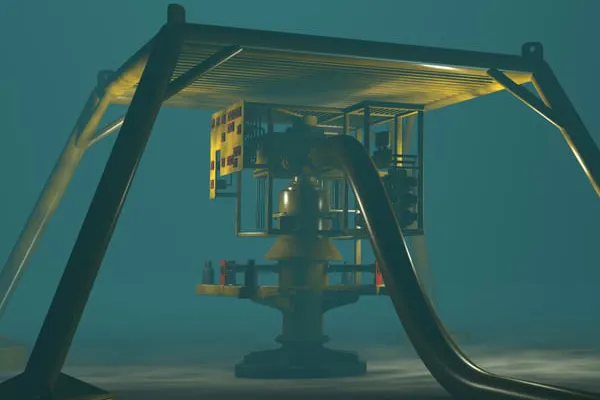
Corrosion
Most corrosion results from a combination of high humidity and salt spray, but some industrial chemicals can also cause corrosion, including various acids and alkaline substances like ammonia.
“Pickering mentioned: ‘To prevent chemical intrusion and dust, electronic devices utilize sealed casings and connectors.’ At the circuit board level, manufacturers apply transparent conformal coatings with thicknesses ranging from 25 to 250 μm. Different materials, including acrylics, polyurethanes, silicone resins, or UV-cured hybrid materials, are used based on specific applications.”
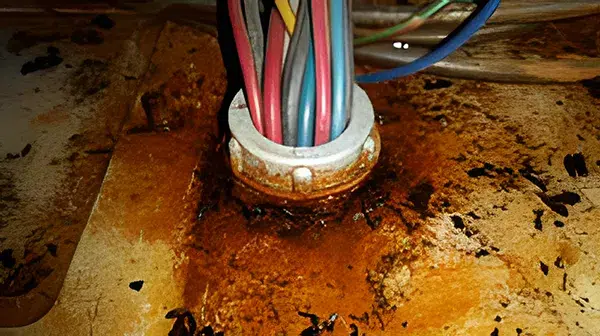
Rough Handling
Sometimes harsh environments have nothing to do with environmental factors such as temperature or pressure. Some connectors are simply subjected to severe wear and tear, possibly because they are dragged, dropped, or coupled and uncoupled multiple times a day. All of these conditions can cause damage that affects the reliability of the connector.
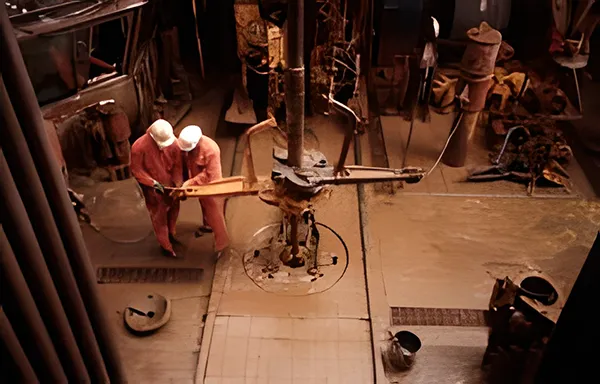
Shock and Vibration
Pickering notes that shock and mechanical vibration are ubiquitous in electronic equipment, causing mechanical stress that can lead to cracked solder joints, metal fatigue and loose fasteners.
What Features Should one Include in a Connector for Harsh Environments?
When selecting connectors for harsh environment, one should pay attention to the following key features:
Material – The material of the connector is crucial to ensure suitability for the specific environment. For instance, in humid or dusty conditions, corrosion-resistant casing plating materials should be chosen.
Proper Sealing – Connectors must exhibit excellent environmental sealing capabilities. Sealed connectors typically perform well against the intrusion of air and gases.
Coupling Methods – Connectors used in harsh environments need to employ durable coupling methods. This may include thread, bayonet, push-pull, latch, or other methods, depending on the application.
IP Protection Rating – Connectors for harsh environments should have an appropriate IP protection rating to resist dust, short-term and prolonged immersion, as well as exposure to high-temperature water and steam.
Considering these features collectively ensures that the connectors perform exceptionally well in extreme environments, ensuring reliability and longevity.